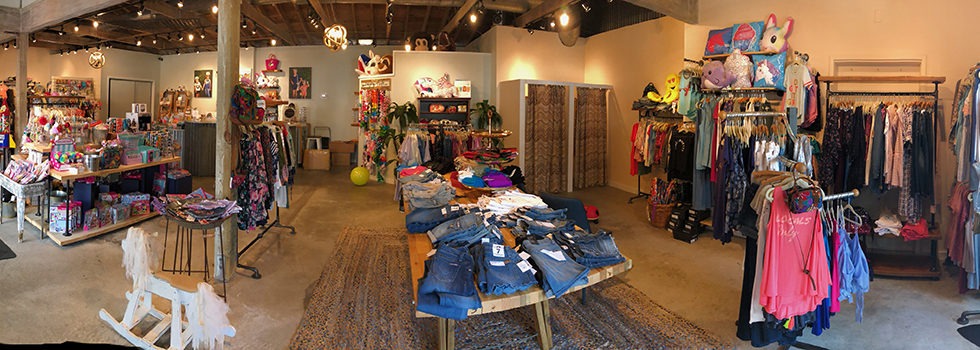
Retail Shipping Just in Time to go Back To School
The Challenge:
A specialty retailer selling high-quality apparel and accessories for children and adults under a variety brands needed to deliver wooden display tables to 620 stores throughout the United States, Puerto Rico and Canada. The “Boy Tables” were intended to display special, new and dated children’s merchandise for a “Back to School” sale, so delivery by a specific date was essential. In addition, the tables had two different finishes, and each store had to get a specific color.
All deliveries had to be by appointment and be two-man, White-Glove and occur before store hours. The delivery team was required to place tables as directed by store management and remove two existing tables at the time of delivery and dispose of offsite.
The Approach:
While originally the shipment was planned and priced as a fully assembled fixture in a crate suitable for normal LTL transport, this is not what actually occurred. Due to production delays, half the tables were shipped from the factory unassembled and not packed. So, in order to maintain a seamless project and not raise the cost of logistics for the client, TechTrans had to work with the fixture vendor to develop and produce assembly instructions to provide to our logistics teams.
TechTrans developed a strategic logistics plan utilizing pad-wrapped trucks equipped with full decking and a team of drivers, which enabled us to triple-deck the unassembled tables. The additional costs TechTrans accrued in assembling the tables and then shipping pad-wrapped were offset by fully utilizing our line-haul truck space. With the full decking on the trucks, TechTrans shipped eight unassembled tables in the space of four assembled tables to the regional destination terminals. To save time, TechTrans assembled the fixtures at the destination terminals just before delivery. By collaborating online, TechTrans was able to quickly develop simple assembly instructions and post them online for the logistics teams to access anywhere in the country.
Each table was pad-wrapped and TechTrans created oversize color coded labels and tags with the color of the table on the label attached to pads and fixtures. TechTrans had the color of the table on all documents and reports for each shipment and required the store manager to specifically sign for the color of the table. This ensured the correct color table arrived to the stores. TechTrans also developed a custom report for this project that the customer received daily.
The Result:
TechTrans completed the project in three weeks as planned. More than 98 percent of the stores received deliveries without issues, 99 percent of the tables arrived on time and all arrived damage free. The customer had all of their new display tables in place, and their old ones removed, in time for the release of the new product and the related back to school sale before classes began.